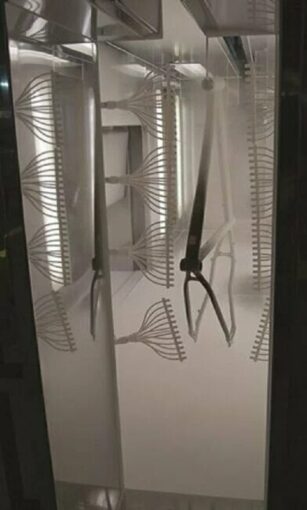
Fig. 1. Spray wall for spraying bicycle frames (Bohemia Bike a.s.)
As the title of the article states, it will discuss the application of powder paints. Specifically, it is about a lesser known and used option for automation and mechanisation of spraying, which is spray walls.
When a large number of identical products are being sprayed and manual spraying becomes too costly or when identical spraying is required on each individual piece, automated spraying is needed. It is common practice to mount a manipulator with one or more guns on each side of a continuous conveyor and hanger cab. With the manipulator, it is possible to use a gun with a limited spray range to cover the entire required height of the sprayed items. However, this solution will not allow the top and bottom horizontal surfaces of the product to be sprayed, or significant irregularities and voids in its vertical surface. These surfaces are deflected or too far away from the spray gun nozzle, which oscillates along the vertical axis.
A more suitable solution is the use of spray walls. These consist of guns with branched sprayers (Figure 1). The sprayers cover the maximum spray height required. Reduction of the height is possible by reducing the spacing of individual guns or by switching off an unnecessary gun. An indisputable advantage is the possibility to adjust the sprayers to follow the shape of the object to be sprayed in longitudinal and transverse direction. Spraying the bottom and top surface of the product is thus no problem (Fig. 2). Special shapes of sprayers can be made to suit the specific product.
Gun holders allow you to point the sprayer where you need it. The holders are usually mounted on a swivel bracket that easily deflects in the event of an accidental collision between the product and the guns, preventing damage to the product and spray equipment. During spraying, the spray guns are at rest against the spray walls.
Manually operated pneumatic system
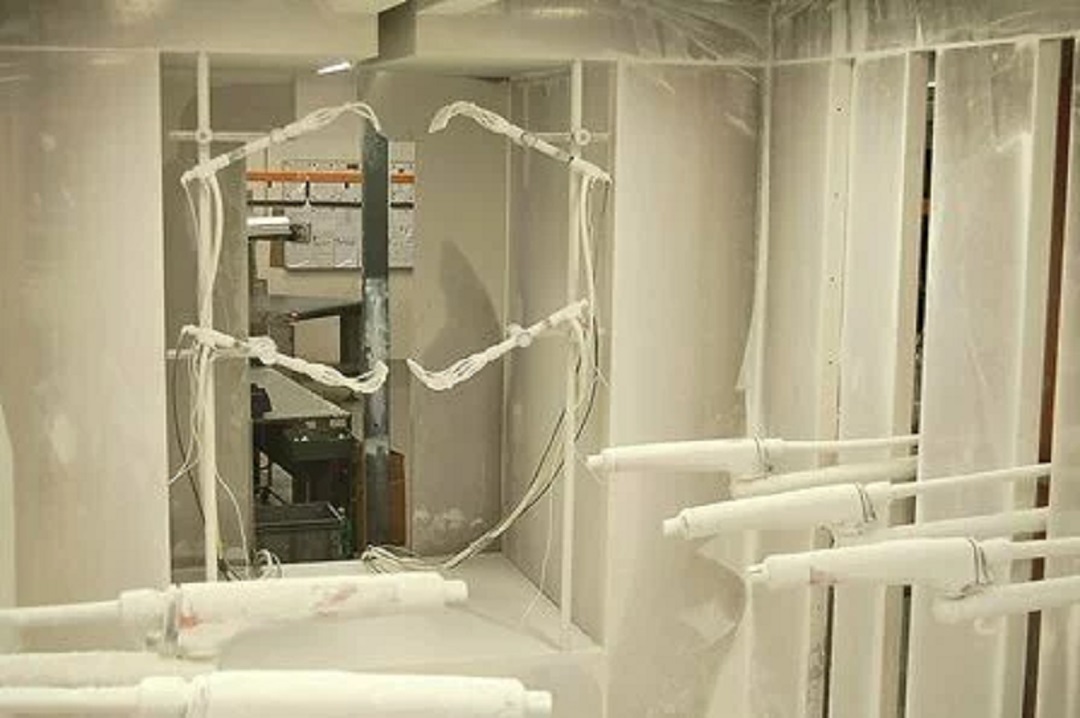
Fig. 2. Sprayers for spraying top and bottom surfaces (ISAN Radiátory, s.r.o.)
There is no unwanted fluctuation in powder feed due to movement of the powder hoses. The stationary gun ensures that the resulting coating does not bear traces of gun oscillation (the gun with manipulator draws an imaginary sinusoid on the sprayed surface). For spray walls, the significant costs of acquiring and operating the manipulator are eliminated. In the case of the simplest version of the spray wall with the so-called tribo guns, we are talking about a purely pneumatic manually operated system without the need for wiring.
In some cases, it may be appropriate to use a belt conveyor instead of a hinged conveyor. This is the case in the operation shown in Figure 3, where the hinge does not prevent the gun from being placed directly over the object. A single sprayer sprays both the top surface and the sides of the article at the same time. For rotating parts, a rotating hanger or table is used (Figure 4). A special, suitably designed spray gun can be used to spray both the cylindrical and front surfaces of the product at the same time.
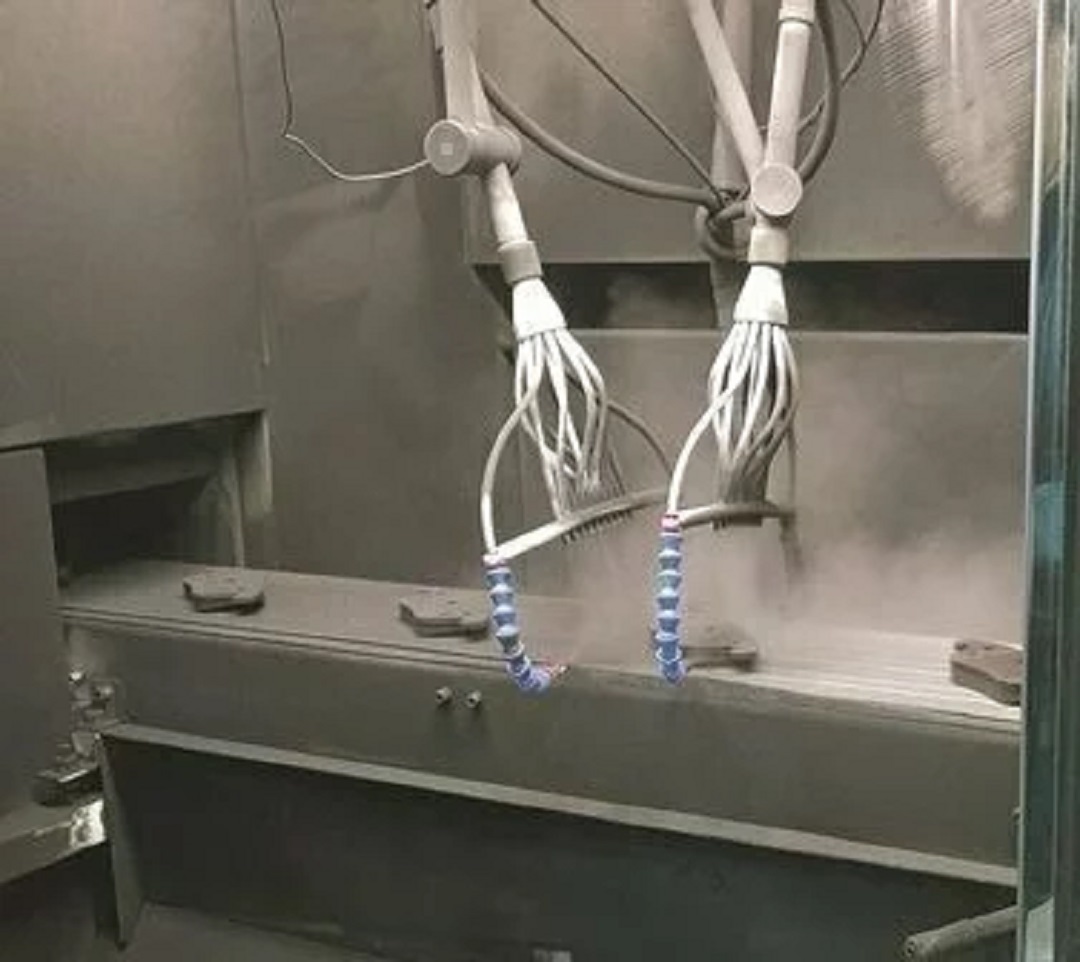
Fig. 3. Special sprayers and conveyor belt (Federal – Mogul Friction Products a.s.)
Powder paint charging forms
The domain of spray walls and branched sprayers is therefore the automatic or mechanised spraying of shaped products for which manipulator guns and single guns with conventional nozzles are not sufficient. It should also be emphasized here that for spraying complex shapes, slots, cavities, etc., a tribo (electrokinetic) system is better suited. This is a method of charging the powder by rubbing it against the charging surface of the gun. The charge gives the powder particles the ability to adhere to a conductive grounded object and stay on it until the time of firing.
Another way the powder gets a charge is by passing through the high intensity electric field generated by the spray gun. This is called electrostatics (corona charging). The electric field acts on the powder flying out of the mouth of the charging tube and prevents it from settling in corners or cavities. Likewise, experience has confirmed that repairs are not possible with this system – electrostatically charged powder is repelled from uncharged areas. In contrast, large flat areas are sprayed evenly and, thanks to the high power that electrostatic guns allow, efficiently. The disadvantage is the higher purchase and operating costs than with tribo guns.
Despite automation, the human factor is essential
If the investor decides to automate, he must also consider the degree of automation. The possibilities of advanced electronics and IT technologies are also penetrating powder coating plants. The most advanced intelligent control systems have their justification in high-volume production, where the complex logistics of the entire coating process, including the differentiation of different types of sprayed product, pre-treatments, different ink firing times, etc., are handled all at once. Air as an elastic medium does not give 100% assurance of the reliability of powder transport and many other unpredictable phenomena (e.g. powder quality) contribute to the final quality of the sprayed surface. Human supervision of the painting process is in most cases necessary. The more complex the system, the more delicate it usually is and requires expert and costly care.
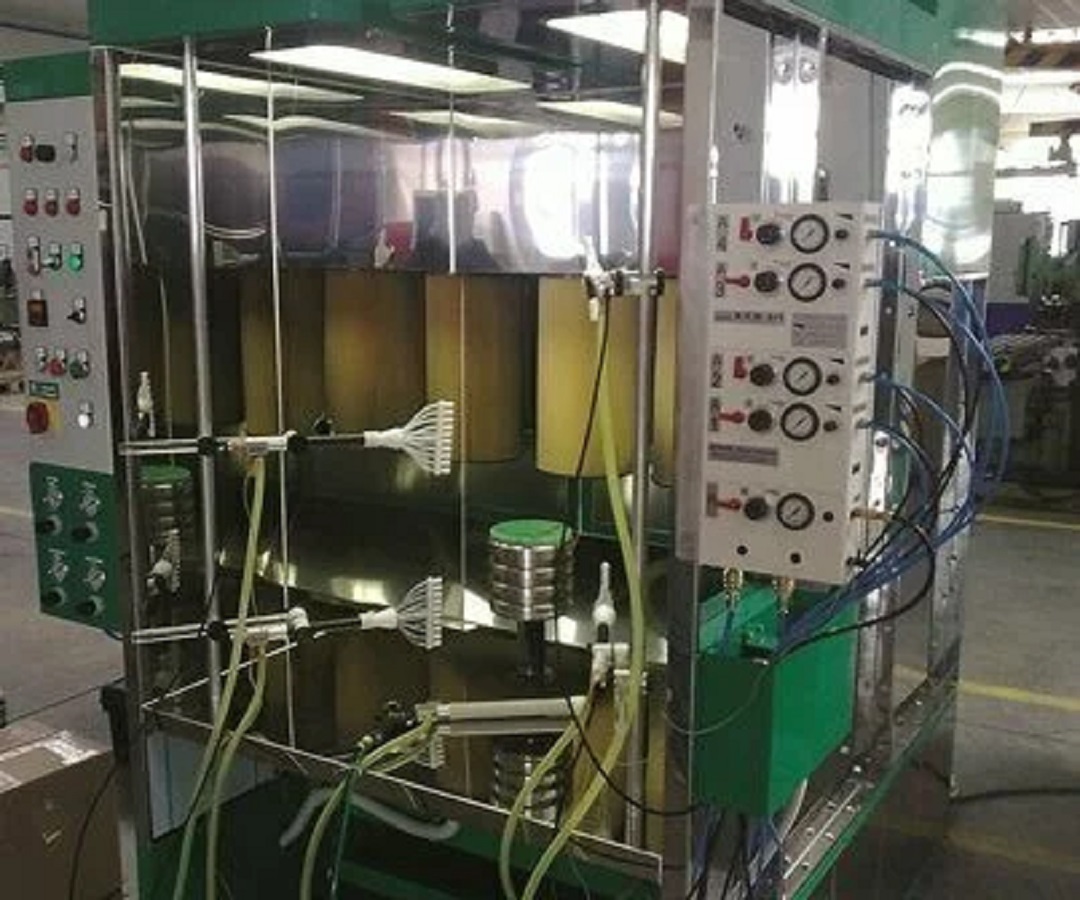
Fig. 4. Automated workstation with turntable (Cebes a.s.)
On the other, basic level of spray automation is the possibility of switching one or all guns with a manual or electric valve. Between these two options, there is a range of possibilities to adapt the system to the actual needs of the production operation. Experienced technology suppliers should educate the investor on all the possibilities and pitfalls of the options and together they should arrive at the ideal solution.
Ing. Petr Vančata
Published in MM Průmyslové spektrum: 2016/12