Any economic balance sheet, especially the cost section, should be based on two starting points, which are one-off and ongoing costs.
One-off costs include mainly investment costs, a significant part of which are project costs, approval procedures, construction of buildings, purchase of machinery and equipment, purchase of know-how, etc. These costs appear after the implementation of the projects for the planned operating period in the form of depreciation. The ratio of the amount of the investment to the expected effect, i.e. above all the measurable labour productivity, certainly matters a great deal, but these funds are amortised according to the tax laws and regulations in force at that particular time and are therefore little susceptible to retrospective effects in the subsequent period. However, what changes over time and what we can influence are the ongoing or operating costs.
Ongoing costs
Ongoing costs change with the market situation for energy, materials and transport and are also only marginally influenced. However, it is always possible to find ways to save overhead, material and energy consumption in our own operations. In short, by organisational measures in the company itself, by rigorously controlling the operation of equipment, and by avoiding time and material losses. Of course, investment costs are included à priori in the ongoing costs, depending on how efficiently we have managed to use the resources invested at the time, given the known technological possibilities. There is no point in worrying about this any longer, it is necessary to start from the current situation.
This article will look at those running costs in powder coating plants that can be influenced in some way. Before we even start spraying powder paint, the following factors already greatly affect the cost-effectiveness of running a paint shop.
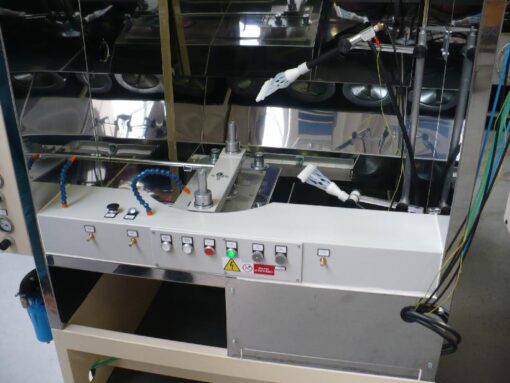
Fig.1: Automatic powder spraying workstation for rotary parts with rotary table.
Choice of blank type and colour shade
If this choice cannot be influenced because the customer (external or internal) does not accept a different type or shade (assembly consistency for parts of one machine sprayed in several paint shops), then there is no reason to consider this issue further. However, if there is room for possible comments on the choice, it is a good idea to remind the customer that some colours are problematic (for example yellow) or have certain surface effects (hammer textures, mats or gloss), as the applied layer thickness and its uniformity are decisive. Similarly, the homogeneity of the temperature field during curing in the oven will affect the final result. Often with these paints we cannot count on the captured overspray being usable for further processing, i.e. spraying.
Price of paint
Different powder paint suppliers have specific characteristics of their products, even though they declare and document the same shade and type of semi-finished product. Price must not and cannot be the only indicator for the selection of a powder coating supplier. Here it is important to talk about the yield per unit weight delivered, for example one kilogram. The yield is significantly influenced by the grading of the powder mass, which means the percentage of particles per unit weight that are of the optimum size for charging (30-40 µm) and thus trapping on the surface to be treated. A considerable range of particle sizes, especially particles below 10 µm, and their high proportion per unit weight make spraying very expensive.
Curing temperature
The effectiveness of spraying powder paints and plastics is also significantly affected by the necessary exposure temperature, where the required chemical and thermal processes occur. The powder manufacturer determines in its laboratories the minimum surface temperature of the object to be sprayed at which reliable bonding of the paint to the substrate occurs after a specific exposure time. Failure to comply may result in insufficient bond with the surface and the coating may sizzle on impact. Subsequent claims management reduces efficiency.
Energy efficiency
Powder coating technologies are generally very energy intensive and therefore there is considerable scope for savings and improvements in the overall energy balance. Powder coatings can be sprayed either on cold surfaces (at ambient temperature – at least 15 °C) or on preheated surfaces of objects at temperatures between 150 °C and 300 °C. The biggest influence on the heat (energy) consumption is the weight of the part and its dimensions. If the choice of treatment technology can be influenced, which is unlikely after investing in the technology, then spraying heavy and bulky cast iron parts is not recommended, as it is not sufficient to heat only the surface layer of the object, but the entire mass must be heated. The heat is dissipated inside the body and may not perfectly bond the layer to the object during curing.
The thermal balance of the curing of the coating will be affected by any heat leakage (imperfection of the insulation, its regular inspection, maintenance of the furnace shell), the shortest possible intervals of opening the inlets, adequate ventilation. When loading sprayed goods into the furnaces using overhead conveyors or loading trolleys, it is necessary to consider how much unused heat escapes with these handling devices. They should be of minimum weight in relation to the weight of the goods being carried (treated) while maintaining sufficient strength and rigidity of the equipment. This means making full use of their handling capacity.
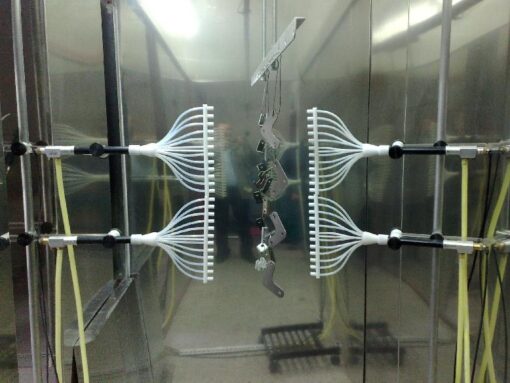
Fig.2: Automatic powder spraying workstation with overhead conveyor and double-sided spraying wall.
Energy saving reserves
The choice of the heating medium for the furnace (electricity, gas, heating oils) was made at the time of investment. However, this does not mean that substitution cannot be considered, given its price on the market and the changed conditions of availability.
The drives of the goods conveyors, the handling of the spray guns and other auxiliary and service equipment, such as the motors of the exhaust fans, sieves and compressed air compressors, are electrically powered in the paint shops. Here there are possible reserves of savings in the sensible and sensible switching off of these appliances.
The transformation of electrical energy into pressurized air energy has low efficiency, making compressed air one of the most expensive forms of energy. Since paint shops usually cannot do without this energy, it is important to manage it well or save it. This starts with regularly checking for air leaks at hose connections and in the distribution pipework. Compressed and conditioned air (free of mechanical impurities, water and oil) is used in particular for spraying and charging powder in the guns, for clarifying (fluidising) powder in the feed tanks (reservoirs), in the pumps for feeding powder into the guns, for vibrating the sieves in the sieves, for cleaning the separation systems and for cleaning all the necessary equipment in the paint shops.
Time availability
The time utilisation of the equipment is directly reflected in the economic efficiency of the paint shop. However, if there is not “enough work”, i.e. the planned and designed capacity is not fully used by producing own semi-finished products or by cooperation for external customers, then the fault is not in the paint shop, but in other departments of the company. Paint shop capacity is a very flexible concept and difficult to define. From a snapshot of the working day for a particular product and spraying equipment, time standards for painting are established. When technological discipline is observed, the aim is not to “rush” the operators of these devices, but not to leave unnecessarily large room for capacity loss.
Labour productivity
In the case of manual workplaces, the technique (art) of spraying strongly influences the productivity of the work (hence the capacity of the workplace). Staffing, as in any other area of human activity, determines not only the quality of the work done, but also the possibilities of production and performance. Here we need to focus our efforts on not wasting human energy, material and physical energy to achieve the same specific goal. There are proven practices where the painter must start spraying on the hardest to reach areas of the parts, and only after they have been applied, work on spraying the easily accessible areas (exterior). This procedure saves not only powder paint, but especially spraying time and claim costs. This working procedure also applies to combination spraying, where part of the surface of the part is sprayed by the machine and the rest by the hand of the painter. Automated spraying is only cost-effective and efficient if the machine sprays at least 70 percent of the surface. A common mistake in such spraying is the so-called “touch-up”, where the part is sprayed by an automatic machine before being sprayed by hand.
It is very difficult to spray hard-to-reach areas, as the part after the machine gun may already be loaded with loose bullets and thus repel the powder from the handgun. The principle is therefore clear. First “pre-spray” difficult to spray surfaces, and then “burn” the surface with the automatic. The way in which the goods are hung or placed during spraying determines the productivity, i.e. the time utilisation of the paint shop. Speeding up the conveyor is not possible due to the necessary minimum spraying exposure times in the booths and curing exposure times in the ovens, and therefore the only way is to minimize the spacing between sprayed parts. However, the density of the parts on the hinges must not be exaggerated to avoid “electrostatic shadows”. Above all, the size of the parts determines the spacing on the conveyor. A tight arrangement can cause an unbearable acceleration of the air current with powder in the gaps between the parts. The minimum edge spacing of the parts is approximately 8 to 10 cm. Electrostatic forces must be given the opportunity to overcome the air eddies at the edges of the parts.
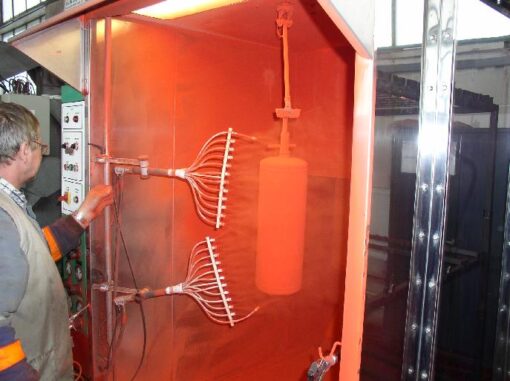
Fig.3: Semi-automatic powder spraying workstation for rotary parts with rotary hinge.
Automation
When automating the spraying process, it is advantageous to use so-called branch sprayers, which do not have a sharp powder exit from the nozzles and can therefore get closer to the object to be sprayed. This not only reduces paint overspray, shortens spraying time, but also directs the spray to hard-to-reach areas. As this spraying technique is not possible with standard paint shop manipulators, I recommend rather spray walls made of branched sprayers, where no movement mechanism is required and the shape of the spray wall can follow the shape of the passing goods. This allows us to get under and over the top spraying surface with the sprayers. This arrangement is not possible when using manipulators. With complex shaped goods, it is possible to quickly reposition or thicken them in the space of a difficult to apply area.
The ideal layout of the spraying workstation for rotary shaped parts consists of hanging the part on a rotating hanger or placing the part on a rotary table. Such workstations with a wall of branched sprayers can be fully automated without manual overspray (see attached pictures).
Consumer materials
Consumable savings can significantly affect the efficiency of powder spraying. The materials used in the surface pre-treatment process, whether it is blast, spray, dip bath degreasing or passivation of the base material, certainly account for the largest share. The removal of these materials from the point of use to the intermediate transport area is influenced by the way the part is suspended. For this purpose, auxiliary technological holes are made in the part for the bath drainage. The regeneration of the used pre-treatment means is also costly, as they are degraded by repeated use. Therefore, it is necessary to save them and prevent their loss, on the other hand, to comply with the recommended treatment parameters in order not to lose money on legitimate claims. Other consumables used in powder coating and paint finishing are binding wires for hanging goods, blanking and masking materials to protect surfaces to be left bare. The savings of these materials can be found in ingenious hanging.
Ing. Josef Ježek
Published in MM Průmyslové spektrum: 2012/04